MTP
ELECTRO-WELDING FLAT GIRDERS MACHINE
MTP series for the mass production of electro-welded flat girders, offering a complete solution for optimising production processes and maximise efficiency.
The MTP 200 version stands out for its high productivity, making it ideal for the most demanding production needs. It can be integrated with customizable stacking systems, which also include optional automatic tying, for complete workflow management.
Key features:
High-precision automatic cutting: ensures impeccable results and minimizes material waste.
State-of-the-art drive and control system: ensures maximum efficiency, speed, and precision.
Elimination of manual operations: reduces cycle times and frees the operator from repetitive tasks.
Optimized and continuous work cycle: increases productivity and the quality of the finished product.
Integration with customizable stacking systems: automates the management of processed material, increasing overall efficiency.
Automatic tying option: speeds up the storage and transport process of trellises.
Benefits:
Increased productivity and reduced production costs
Improved quality of the finished product
Reduction of manual errors and increased safety
Optimization of workflow and efficient space management
Flexibility to meet different production needs
MTP electro-welded truss girder machine is the ideal choice for the production of electro-welded truss with maximum efficiency and precision.
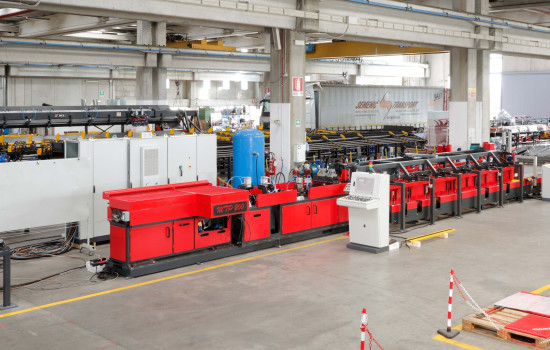
MTP 200
ELECTRO-WELDING TRUSS GIRDER MACHINE
Workable wire diameters:
Longitudinal wire ∅4 - ∅8 mm / 5/32"-1/4"
Zigzag wire ∅6,5 mm / 5/32"-1/4"
• Constant de-coiling
• Adjustable straightening for "zig-zag" and wires with 3 orthogonal roller groups
• Uniform and symmetrical trusses with “zig-zag” forming machine: independent management of wires and adjustable height
• Highly efficient and productive welding with controlled profile technology and 2 independent units
• Synchronised movement and fixed pitch feed for uniform and symmetrical trusses
• Precise cutting to size
• Automatic stacking
• Automatic tying
Request information